Injection molding is a widely used manufacturing process for producing plastic parts with high precision and efficiency. To maintain optimal performance, precise temperature control is crucial throughout the molding cycle. One of the most reliable heating solutions for this process is cartridge heaters. These compact, high-watt density heaters provide the necessary heat for molds, manifolds, and nozzles, ensuring consistent material flow and quality part production.
How Cartridge Heaters Work in Injection Molding
Cartridge heaters are cylindrical heating elements designed to fit into drilled holes within metal parts, such as mold plates or hot runner systems. When energized, they generate heat through a resistive wire element embedded in an insulating ceramic core. The heat is then transferred efficiently to the surrounding metal, maintaining a stable and uniform temperature essential for precise injection molding operations.
Key Applications of Cartridge Heaters in Injection Molding
- Mold Heating: Cartridge heaters are inserted into molds to maintain a consistent temperature, preventing material cooling too soon and ensuring uniform part formation.
- Hot Runner Systems: These heaters keep the plastic material in a molten state as it travels through the manifold and nozzles, reducing material waste and improving cycle times.
- Nozzle Heating: Properly heated nozzles allow for smooth injection of molten plastic, preventing premature solidification and ensuring complete cavity filling.
- Gate and Sprue Heating: Heating elements at gates and sprues help regulate flow, reducing defects like short shots and incomplete fills.
Benefits of Using Cartridge Heaters in Injection Molding
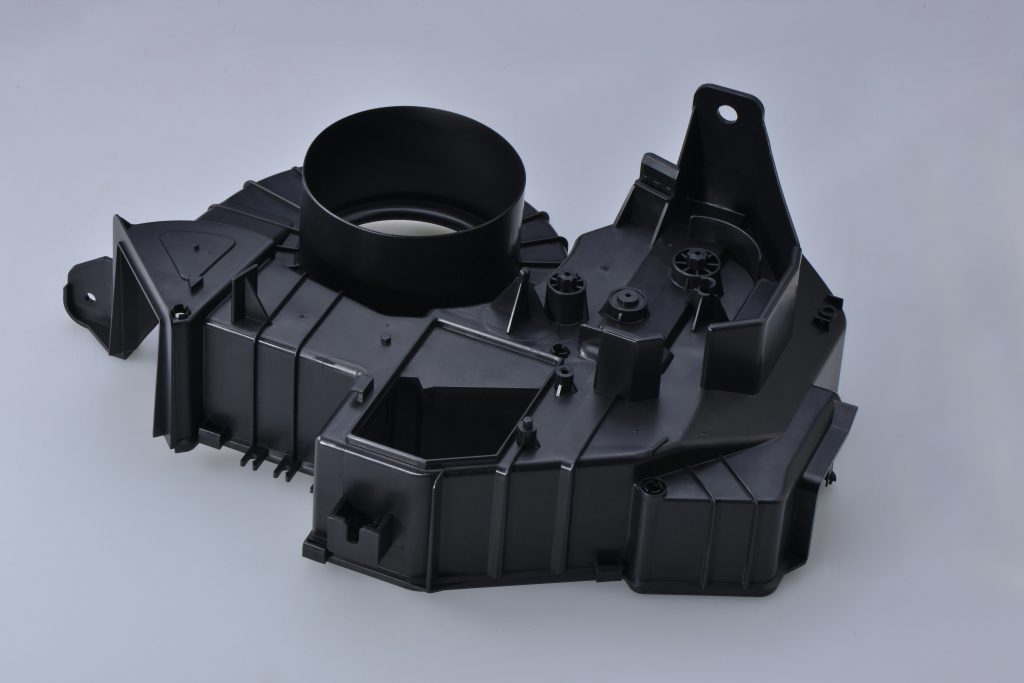
- Precise Temperature Control: Advanced cartridge heaters come with built-in thermocouples, allowing real-time temperature monitoring and adjustments to prevent overheating or material degradation.
- High Watt Density: The compact design allows for high wattage in a small footprint, delivering rapid heating and maintaining consistent mold temperatures.
- Durability and Longevity: Made from stainless steel and other robust materials, cartridge heaters withstand harsh molding environments, including high pressure and repeated thermal cycling.
- Energy Efficiency: Efficient heat transfer reduces power consumption while maintaining optimal processing temperatures, lowering overall operational costs.
- Improved Part Quality: By eliminating cold spots and temperature variations, cartridge heaters ensure better material flow and reduce defects such as warping, sink marks, and voids.
Choosing the Right Cartridge Heater for Your Application
When selecting a cartridge heater for injection molding, consider the following factors:
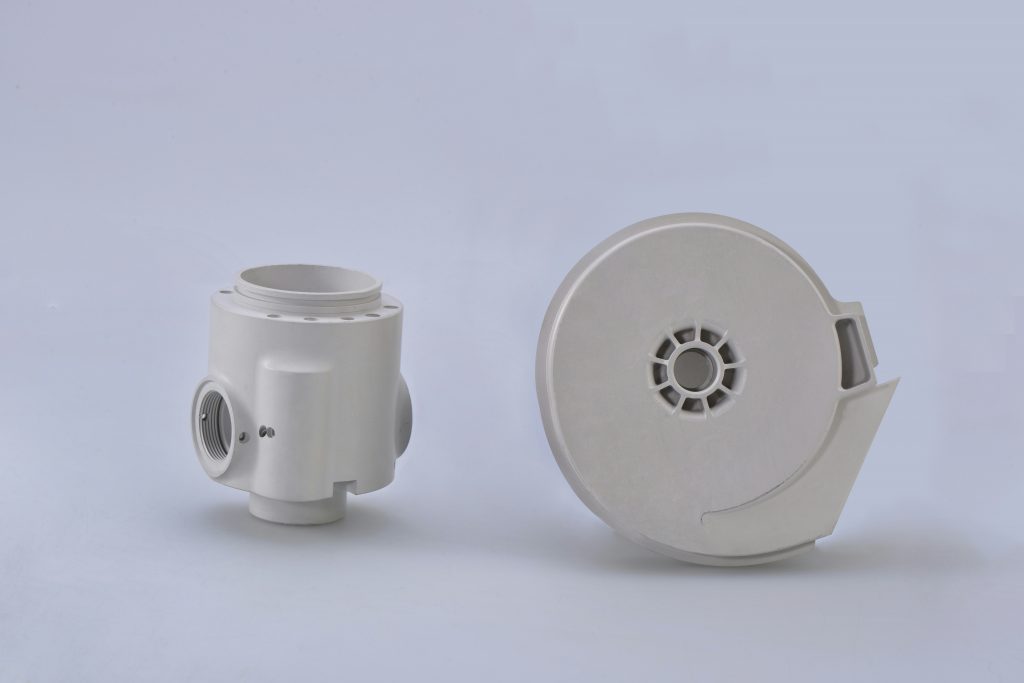
- Size and Fit: Ensure the heater diameter and length match the drilled hole for optimal heat transfer.
- Wattage and Voltage: Choose appropriate watt density based on the application’s heating requirements.
- Lead Configuration: Different terminations, such as high-temperature leads or right-angle exits, may be required for ease of installation.
- Material Compatibility: Stainless steel sheathing provides excellent resistance to oxidation and corrosion, making it ideal for injection molding environments.
Conclusion
Cartridge heaters play a vital role in injection molding by ensuring precise and efficient heating throughout the process. Their durability, high watt density, and precise temperature control make them indispensable for mold heating, hot runner systems, and nozzle applications. By selecting the right heater specifications and maintaining proper temperature management, manufacturers can enhance product quality, reduce cycle times, and improve overall efficiency in injection molding operations.
For high-performance cartridge heaters tailored to your injection molding needs, explore our range of industrial heating solutions today!